“The idea of conducting tours at one of our manufacturing facilities came to me when a colleague suggested that visiting the truss plant would give her a better understanding of the truss orders she processes on a daily basis,” explains BeLit Safety Coordinator Bobby Harrison.
The idea was such a good one, all employees working outside of the manufacturing process were given the chance to see what happens after a design is done and before it gets invoiced. “A lot of individuals working for Apex and TDS spend countless hours on projects for our customers, but never get the opportunity to see the manufacturing side of the business or the finished product,” Bobby points out.
For three weeks in May, Bobby organized facility tours at the True House facility in Jacksonville for anyone who wanted to attend. Over the course of three weeks, 25 BeLit, Apex, and TDS employees were able to see the truss manufacturing operation. “The interest in this opportunity was outstanding,” reports Bobby.

Visiting employees met True House office staff and learned about the roles they play in ensuring trusses get built and delivered to our customers based on their needs. Next, employees were shown roof building, floor building, and material building. Plant Manager Sean Davies, Day Shift Supervisor Michael Wright, and Safety and QC Coordinator Darryl Moore joined Bobby during the course of these tours to help explain the truss building process from beginning to end and to answer visitors’ questions.
“The visits were great!” says Darryl. “They allowed the Apex and TDS employees to see all the hard work the True House employees put in to turn their efforts into a finished product.”
Michael agrees: “It felt good to see the design team interested in the daily processes as well as the struggles at the fabrication level.”
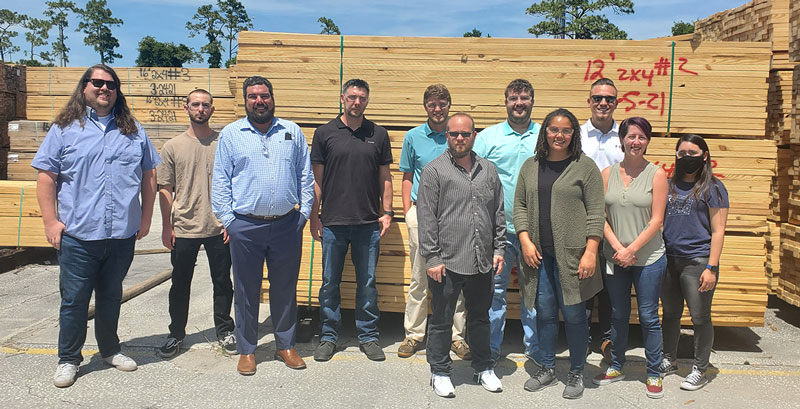
“We were excited to see the unity between our companies,” Sean adds. “It paints a bigger picture in the production throughput from design to product delivery. Many of the individuals asked excellent questions pertaining to design vs. fabrication.”
The overall response was very positive and employees were appreciative for the opportunity to gain a new perspective on the company’s product. “You don’t get a true understanding of how big trusses actually are until you see them in person,” says Michael Blount, a truss designer at Apex.
“I think we should offer the same opportunity to the True House employees and allow them to visit the BeLit office to see the hard work that goes into the designs of the trusses they produce on a daily basis,” adds Darryl.
Bobby agrees that this is just the beginning: “Who knows? Maybe one day we will be able to charter all the employees down to the Crescent City facility to see our most prized possession…the Randek Autoeye!”